Application des géosciences aux défis les plus importants de l’Australie
Introduction
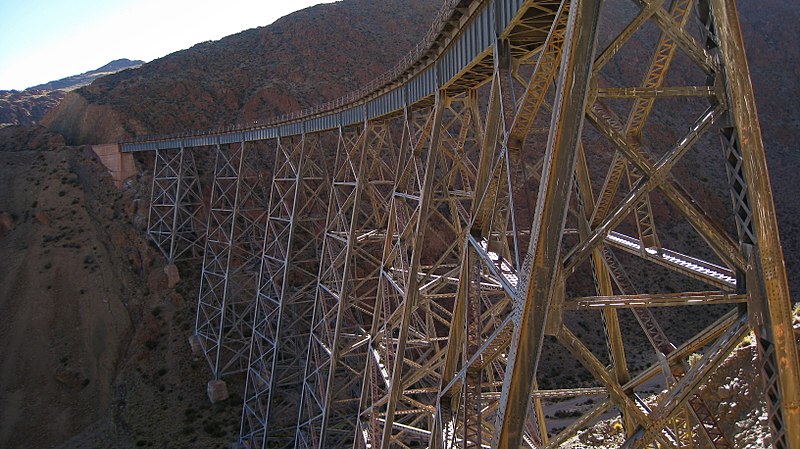
Pont en acier. Source : Wikimedia Commons
Le fer est l’épine dorsale du monde que nous avons construit autour de nous et c’est l’ingrédient de base de l’acier (fer plus carbone). Le fer est un métal très utile car il peut être mélangé à d’autres métaux pour obtenir toute une variété d' »alliages » encore plus résistants, qui ne rouillent pas facilement et peuvent être façonnés en produits allant des voitures aux épingles, des appareils ménagers aux bâtiments, des ponts aux chemins de fer, des boîtes de conserve aux outils. En bref, nous dépendons du fer (sous forme d’acier) pour fabriquer presque tout ce dont nous avons besoin pour vivre au XXIe siècle. Aujourd’hui, nous utilisons vingt fois plus de fer (sous forme d’acier) que tous les autres métaux réunis.
Le fer (Fe) est l’un des éléments formant des roches les plus abondants, constituant environ 5 % de la croûte terrestre. C’est le quatrième élément le plus abondant après l’oxygène, le silicium et l’aluminium et, après l’aluminium, le métal le plus abondant et le plus largement distribué. Le champ magnétique de la Terre est dû au fer (et au nickel) présent dans son noyau, de sorte que lorsque nous utilisons une boussole, nous nous servons du fer qui se trouve sous nous. Le fer est un métal gris argenté qui rouille rapidement lorsqu’il est exposé à l’air et à l’eau. Il est à l’origine de la couleur rouge de beaucoup de nos roches et des sables rouges profonds des déserts australiens. Le fer ne se trouve généralement pas à l’état pur au sein des roches, il est plutôt combiné à l’oxygène dans les minéraux de minerai tels que l’hématite (du mot grec signifiant » pierre de sang « ).
Propriétés
Dans la croûte terrestre, le fer se trouve principalement sous forme de minéraux d’oxyde de fer tels que l’hématite, la magnétite, la goethite et la limonite. Les minéraux les plus utilisés comme minerai pour fabriquer du fer sont l’hématite (Fe2O3) et la magnétite (Fe3O4). Le fer est assez mou et facile à travailler, mais son point de fusion est très élevé (1538°C). Le fer et certains alliages de fer sont également magnétiques.
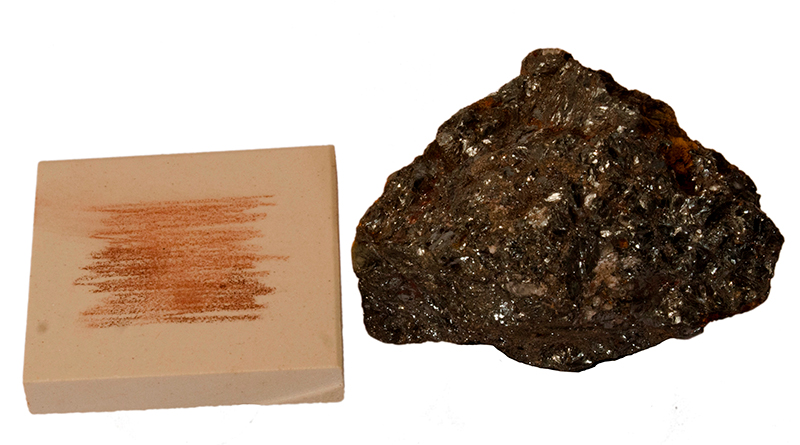
Hématite et poudre d’hématite sur plaque striée. Source : Geoscience Australia
Le fer est environ huit fois plus lourd que l’eau (sa densité relative est de 7,87). Lorsque le fer est exposé à l’air, il commence à se retransformer en oxyde de fer et la poudre rouge qui se forme à la surface du fer est ce que nous appelons la rouille. Vous avez peut-être vu de la rouille sur de vieilles voitures ou de vieux hangars en fer. Pour rendre le fer plus solide et moins susceptible de rouiller, on peut le combiner avec du carbone et d’autres éléments pour obtenir de l’acier. L’acier est l’un des produits les plus recyclés au monde : environ 60 % de l’acier disponible pour le recyclage est réintégré dans la fabrication de nouvel acier.
Les propriétés du fer |
|
---|---|
Symbole chimique |
Fe, vient du mot latin pour le fer ferrum |
Ore |
Les oxydes de fer, par ex.par exemple l’hématite et la magnétite |
Densité relative |
7.87 g/cm3 |
Dureté |
4 sur l’échelle de Mohs |
Malléabilité |
Haute |
Haute |
|
Point de fusion |
1538°C |
Point d’ébullition |
2862°C |
Utilisations
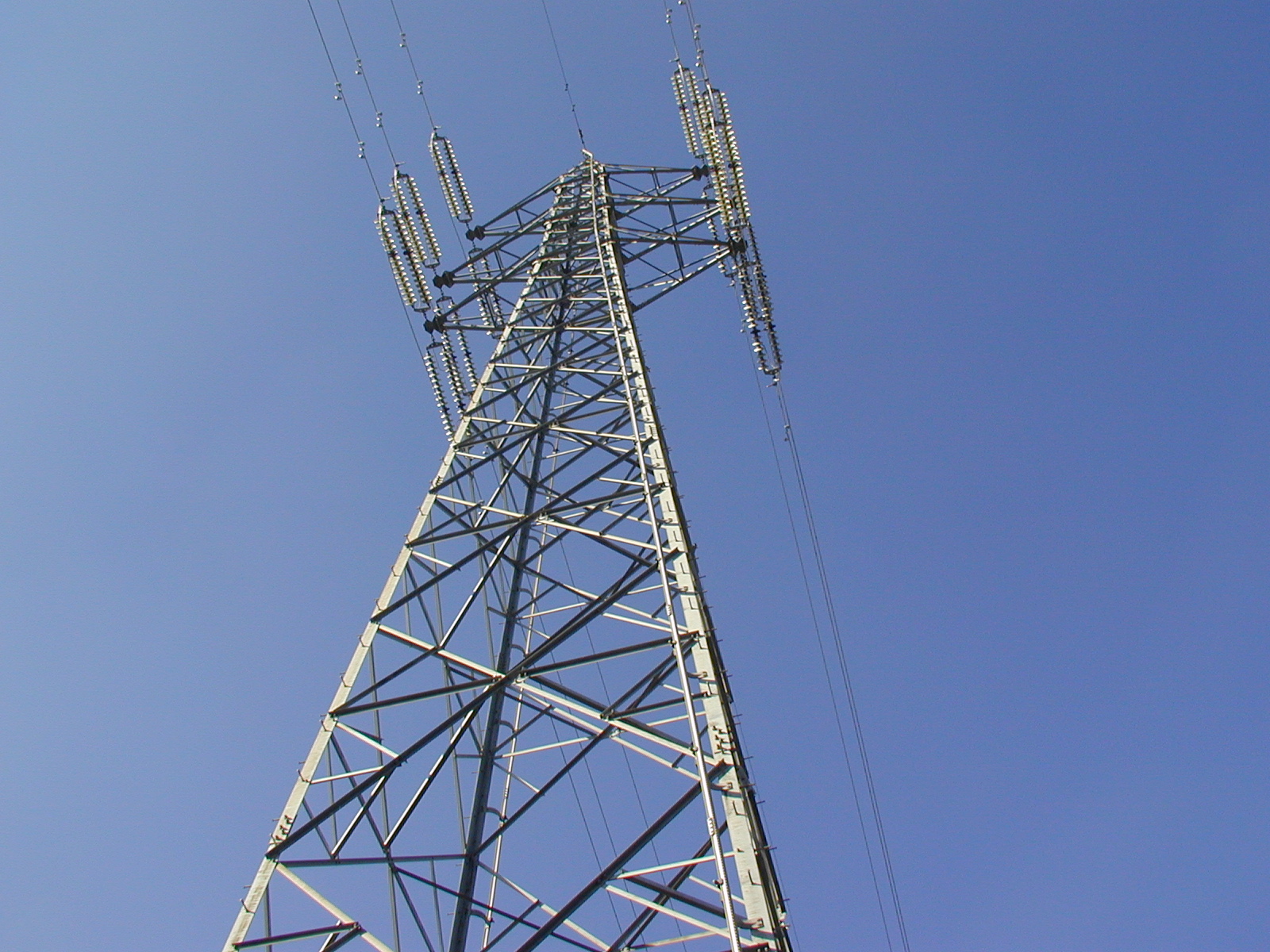
Pylône en acier suspendant des lignes électriques aériennes. Source : Wikimedia Commons
Environ 98% de la production mondiale de minerai de fer est utilisée pour fabriquer du fer sous forme d’acier. Le fer sous forme de fonte a de nombreux usages spécifiques (par exemple, tuyaux, raccords, blocs moteurs) mais le fer pur est assez mou. L’ajout d’une petite quantité de carbone (généralement moins de 1 %) transforme le fer en acier, qui est nettement plus dur et extrêmement polyvalent. Il existe de nombreux types d’acier fabriqués en ajoutant du carbone et d’autres éléments tels que le chrome, le manganèse, le nickel et le molybdène pour former une gamme d’alliages aux propriétés différentes (par exemple, l’acier inoxydable). En modifiant les proportions de ces éléments supplémentaires, il est possible de fabriquer des aciers adaptés à une grande variété d’utilisations. Le tableau ci-dessous présente les propriétés et utilisations particulières de certains composés du fer.
Nom du composé de fer | principaux composants | propriétés | usages |
Fonte |
fer + jusqu’à 5% de carbone |
Ils se corrodent facilement |
fours de camp |
Fonte galvanisée |
Fonte + revêtement de zinc |
résiste à la rouille . |
toiture |
---|---|---|---|
Tôle d’étain | fer + revêtement d’étain | résiste à la rouille | boîtes d’étain pour la conservation des aliments |
Acier |
fer + moins de 1% de carbone |
dur |
bâtiments |
Stainless inoxydable |
fer + |
ne rouille pas |
coutellerie |
dans le monde entier. équipements hospitaliers pièces automobiles |
Acier à outils |
fer + |
très dur |
outils de coupe en métal |
Les propriétés souhaitables de l’acier et son coût relativement faible en font le principal métal de structure dans les projets d’ingénierie et de construction, Il représente environ 90 % de tous les métaux utilisés chaque année. Environ 60 % des produits en fer et en acier sont utilisés dans le transport et la construction, 20 % dans la fabrication de machines, le reste étant utilisé dans les boîtes de conserve et les conteneurs (dans les industries du pétrole et du gaz) et dans divers appareils et autres équipements, voir le tableau ci-dessous pour d’autres utilisations du fer et de l’acier.
Utilisation | Description |
Transports |
C wagons/moteurs en acier, navires, châssis de voitures, cylindres de moteurs. |
Construction |
Bâtiments en acier, ponts (comme le pont du port de Sydney), armature des bâtiments en béton, toitures, bardages, portes, clôtures. |
---|---|
Machines |
Moteurs en acier, pompes, grues, équipements d’atelier (ex. outils de coupe, trépans). |
Produits en fil métallique |
Clôtures en fil d’acier, câbles de navires, agrafes, moustiquaires de portes, écrous & boulons. |
Stockage |
Contenants alimentaires en acier, réservoirs de stockage. |
Pétrole et gaz |
Tiges de forage, tubages, pipelines en acier. |
Appareils et équipements |
Réfrigérateurs en acier, machines à laver, lave-vaisselle, couverts, équipements hospitaliers. |
Le fer pur est nécessaire à la bonne croissance des plantes. Les animaux ont besoin de fer pour fabriquer de l’énergie et transporter le sang dans le corps (les aliments riches en fer sont la viande rouge et le foie, le jaune d’œuf et les légumes verts à feuilles). Le fer a été le premier élément à être reconnu comme essentiel pour les personnes. En 1681, un médecin a utilisé avec succès le fer pour traiter des patients qui étaient pâles, manquaient d’énergie et souffraient d’anémie. Le chlorure de fer est utilisé dans le traitement et la purification de l’eau. |
Fun |
La limaille de fer est utilisée dans les ‘sparklers’. |
Électronique |
Le chlorure de fer est utilisé pour graver le cuivre dans la fabrication des circuits imprimés électriques. |
Cuisine |
Fours de camp et woks en fer forgé. |
Décoration |
Mobilier d’extérieur en fer forgé, rampes de porche et autres articles décoratifs. |
Histoire
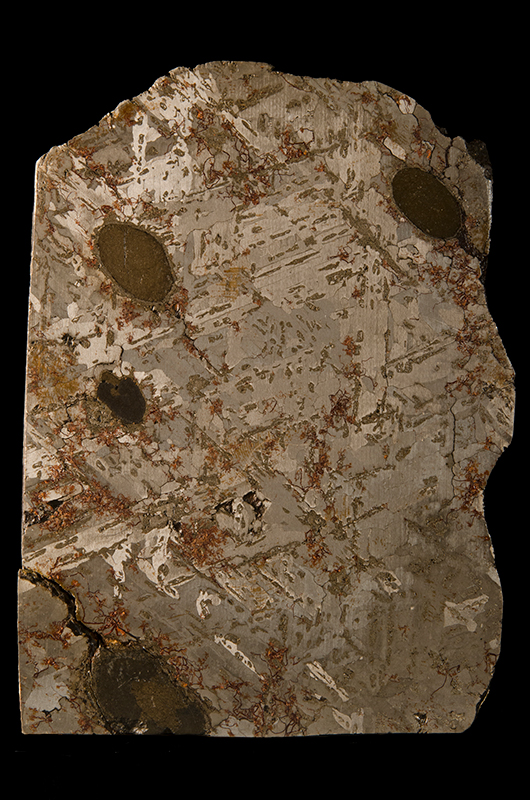
Météorite de Coolac – météorite de fer. R21381. Source : Geoscience Australia
Le fer fait partie des plus anciens métaux connus des humains. L’Homme paléolithique utilisait l’hématite finement broyée comme peinture corporelle. Vers 4000 avant J.-C., les Égyptiens et les Sumériens ont utilisé pour la première fois le fer provenant de météorites pour fabriquer des perles, des ornements, des armes et des outils. La chronologie de l’âge du fer varie selon les régions ; par exemple, les Hittites forgeaient le fer (ils le chauffaient, le martelaient, puis le refroidissaient rapidement pour produire un fer plus dur que le bronze que les gens utilisaient auparavant) entre 1300 et 1100 avant J.-C. De même, selon Tewari (2003), les preuves archéologiques indiquent que le travail du fer en Inde s’est déroulé entre 1800 et 1000 avant J.-C. À l’époque de l’Empire romain, le fer était utilisé pour les lits, les portes, les chars, les clous, les scies, les haches, les lances, les hameçons et les outils d’affûtage. Au Moyen Âge, avec l’introduction du canon en fer et du boulet de canon, la consommation de fer a augmenté pour dépasser le cuivre et le bronze comme métal le plus utilisé. À la fin du XIXe siècle, l’âge de l’acier a commencé, avec les bateaux en bois qui ont cédé la place à l’acier, l’arrivée des machines dans les usines et l’invention du chemin de fer. Le fer est indispensable à la civilisation moderne et les hommes savent l’utiliser depuis plus de 3 000 ans. Cependant, son utilisation ne s’est généralisée qu’au 14e siècle, lorsque les fours de fusion (ancêtres des hauts fourneaux) ont commencé à remplacer les forges.
Formation
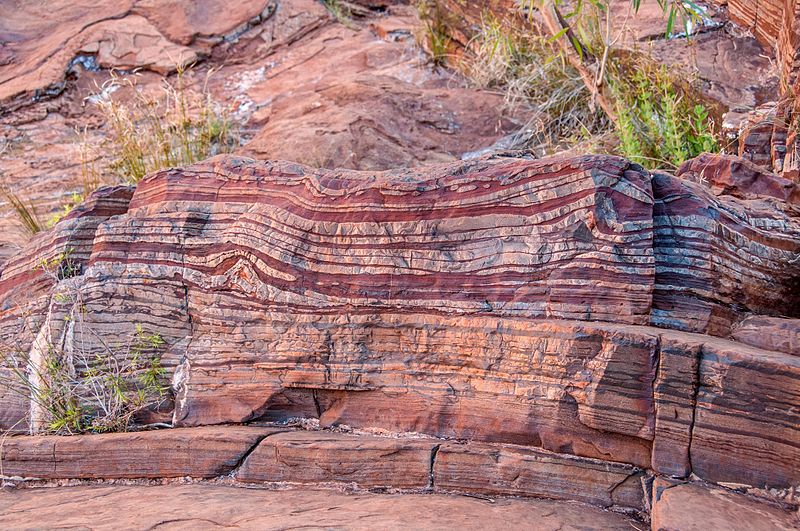
Formation de fer en bandes à Fortescue Falls, Australie occidentale. Source : Wikimedia Commons
Les minerais de fer sont des roches dont le fer métallique peut être extrait de manière économique. La plupart des gisements de minerai de fer dans le monde se trouvent dans des roches connues sous le nom de formations de fer en bandes (BIF). Ce sont des roches sédimentaires qui présentent des couches alternées de minéraux riches en fer et d’une roche siliceuse à grain fin appelée chert.
Plusieurs des formations de fer en bandes exploitées aujourd’hui se sont formées il y a des millions d’années. Il y a environ 3000 millions d’années, il n’y avait pas ou très peu d’oxygène dissous dans les océans. Cependant, les océans contenaient beaucoup de silice dissoute, provenant de l’altération des roches. De temps à autre, cette silice précipitait dans l’eau de mer sous forme de couches de gelée de silice, qui durcissaient lentement pour devenir la roche que nous appelons chert. L’oxyde de fer soluble était également produit par l’altération des roches et était également rejeté dans la mer par les rivières.
Il y a environ 2500 millions d’années, les océans étaient habités par des bactéries qui ont développé la capacité de photosynthétiser et de produire de l’oxygène. Il y avait des « efflorescences » saisonnières qui libéraient d’énormes quantités d’oxygène dans l’eau de mer qui réagissaient avec l’oxyde de fer soluble pour former de l’oxyde de fer insoluble. Celui-ci a précipité hors de la solution sous la forme des minéraux magnétite et hématite formant des couches de fer parmi les autres couches de sédiments au fond de la mer.
Pendant plusieurs millions d’années, ces processus de précipitation de la silice et de l’oxyde de fer se sont répétés à l’infini entraînant le dépôt de couches alternées de chert, d’hématite et de magnétite. Le nom de formation de fer en bandes vient de la couleur caractéristique de ces énormes dépôts. Le processus s’est poursuivi pendant près d’un milliard d’années et a fini par laisser s’accumuler l’oxygène dans l’atmosphère.
Ressources
La plupart des ressources importantes de minerai de fer dans le monde se trouvent dans des formations de fer en bandes, qui sont presque exclusivement d’âge précambrien (c’est-à-dire âgées de plus de 541 millions d’années). Les formations de fer en bandes sont présentes sur tous les continents.
Le fer a été le premier métal à être découvert en Australie par l’explorateur Edward John Eyre dans les Middleback Ranges en Australie-Méridionale. Bien que des ressources en minerai de fer soient présentes dans tous les États et territoires australiens, près de 90 % des ressources identifiées se trouvent en Australie occidentale, dont près de 80 % dans la province de Hamersley, l’une des principales régions productrices de minerai de fer au monde. L’Australie est l’un des plus grands producteurs de minerai de fer au monde et le minerai de fer est la base de l’une des principales industries d’exportation de l’Australie.

Les principaux gisements et mines de fer de l’Australie (2016). Source : Geoscience Australia
Dans les Hamersley Ranges, dans le district de Pilbara en Australie occidentale, il existe trois principaux types de gisement de fer : les enrichissements en oxydes de fer au sein des FIF, par ex. Mt Tom Price ; les oxydes de fer déposés le long d’anciens chenaux fluviaux, principalement d’âge tertiaire (paléochenaux) ; et les dépôts d’oxydes de fer formés à partir de l’érosion de corps minéralisés existants (dépôts de minerai de fer détritique).
Les dépôts d’enrichissement BIF comprenant de l’hématite et de l’hématite goethite sont les plus importants en ce qui concerne les ressources et la production. La teneur en fer de ces minerais est très variable et, jusqu’à récemment, la plupart des gisements devaient avoir une teneur moyenne de plus de 60% de fer pour que l’exploitation soit commercialement viable. Cependant, certains gisements peuvent maintenant avoir des teneurs en fer comprises entre 56 % et 59 % et être commercialement viables. Les gisements d’enrichissement BIF se trouvent en Australie occidentale dans le Pilbara (par exemple Yarrie), et le bloc Yilgarn (par exemple Koolyanobbing) et en Australie du Sud (par exemple Iron Duke, Middleback Range). Les dépôts de paléochenaux composés de limonite pisolitique sont les suivants en importance et sont appréciés pour leur faible teneur en impuretés telles que le phosphore. Ils ne sont pas aussi riches en fer que les minerais d’enrichissement BIF. Ceux qui sont exploités contiennent généralement 57 % à 59 % de fer. Les gisements de minerai de fer détritique se trouvent en aval des gisements d’enrichissement BIF dont ils ont été érodés. Ils sont généralement faciles à récupérer et ont une teneur comprise entre 40 % et 55 % de fer.
Plus d’informations sur les ressources et la production.
Mining
Formation de fer en bandes à Fortescue Falls, Australie occidentale. Source : Wikimedia Commons
La plupart des minerais de fer exploités aujourd’hui comprennent les minéraux d’oxyde de fer que sont l’hématite, Fe2O3 (70% Fe) ; la goethite, Fe2O3s H2O, (63% Fe) ; la limonite, un mélange d’oxydes de fer hydratés (jusqu’à 60% Fe) ; et la magnétite, Fe3O4 (72% Fe). Comme pour la plupart des mines de minerai de fer dans le monde, toutes les principales mines de minerai de fer australiennes sont exploitées à ciel ouvert. La roche contenant le minerai de fer est d’abord extraite à l’explosif et creusée dans des mines à ciel ouvert. Les minerais des principales mines de la région de Pilbara, en Australie occidentale, sont transportés des fronts de taille aux installations de concassage et de criblage par des camions pouvant transporter plus de 300 tonnes. Il existe trois grands producteurs de minerai de fer dans la région de Pilbara : BHP Billiton Ltd (BHP), Rio Tinto Ltd (Rio) et Fortescue Metals Group Ltd (FMG).
Traitement
Le traitement du minerai d’hématite et de magnétite comprend le concassage, le criblage et le broyage pour produire des morceaux et des fines d’hématite. Le minerai de magnétite est ensuite traité par séparation magnétique, un processus important dans la production de concentré de fer magnétite.
La concentration comprend tous les processus qui vont augmenter (améliorer) la teneur en fer d’un minerai en éliminant les impuretés. La valorisation, terme un peu plus large, comprend ces procédés ainsi que ceux qui rendent un minerai plus utilisable en améliorant ses propriétés physiques (par exemple, le pelletage et le frittage). De nombreuses mines de minerai de fer recourent à une certaine forme d’enrichissement pour améliorer la teneur et les propriétés de leurs produits. Dans de nombreuses mines en exploitation, notamment Mount Tom Price, Paraburdoo, Mount Whaleback et Christmas Creek, des installations de traitement du minerai ont été construites pour permettre l’enrichissement des minerais de fer à faible teneur, y compris les minerais qui ont été contaminés par du schiste, afin qu’ils soient exploités et, après amélioration, vendus comme produits à haute teneur.
La pelletisation est un procédé de traitement utilisé pour les minerais très fins ou pulvérulents. Les pellets constituent une alimentation idéale pour les hauts fourneaux car ils sont durs et de taille et de forme régulières. En Australie, les concentrés pompés à Savage River sont pelletisés à Port Latta pour être expédiés vers les marchés nationaux et étrangers et les minerais fins de Middleback Range sont pelletisés avant d’être fondus dans le haut fourneau de Whyalla.
Le frittage est un procédé utilisé pour agglomérer les fines de minerai de fer en vue de la fusion en haut fourneau et est généralement effectué dans les centres sidérurgiques. Il implique l’incorporation de calcaire broyé, de coke et d’autres additifs disponibles dans les opérations sidérurgiques. Ces additifs comprennent les déchets extraits des gaz d’échappement des fours, la calamine produite lors des opérations de laminage et les fines de coke produites lors du criblage du coke.
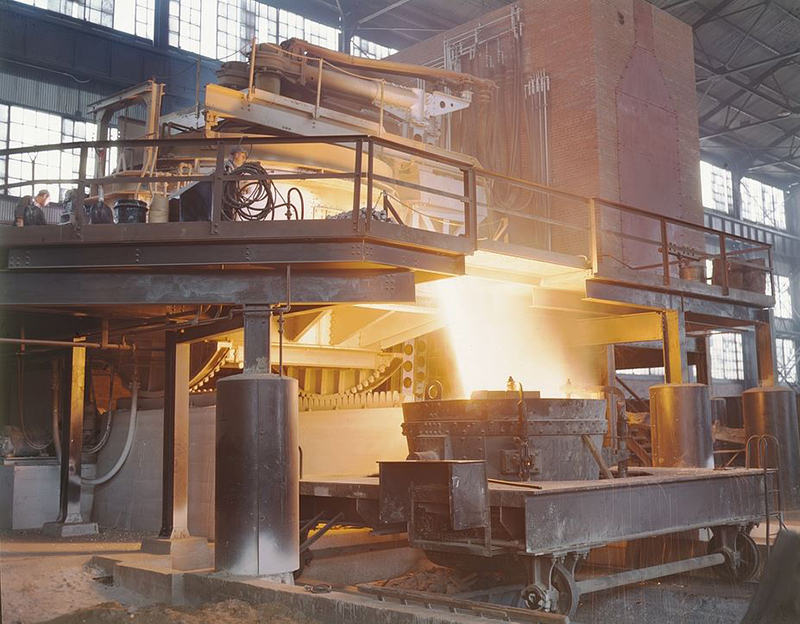
Acier chauffé à blanc se déversant d’un four à arc électrique. Source : Wikimedia Commons
Le fer brut est une étape intermédiaire dans la production d’acier et est produit par la fusion du minerai de fer (généralement sous forme de morceaux, de boulettes ou d’agglomérés) dans des hauts fourneaux. En Australie, les hauts-fourneaux sont situés à Port Kembla et à Whyalla. L’élimination, par oxydation, des impuretés présentes dans la fonte brute, telles que le silicium, le phosphore et le soufre, et la réduction de la teneur en carbone, aboutissent à la production d’acier.
L’ajout de métaux tels que le nickel, le chrome, le manganèse ou le titane confère à l’acier des propriétés particulières comme la résistance électrique et la résistance à l’usure, à la rouille, aux chocs ou à la dilatation lorsqu’il est chauffé.L’acier refroidi est façonné et peut être revêtu d’étain, de zinc ou de peinture pour l’aider à se protéger de la rouille, créant ainsi des produits tels que le Zincalume et le Colorbond.