Aplicar a geociência aos desafios mais importantes da Austrália
Introdução
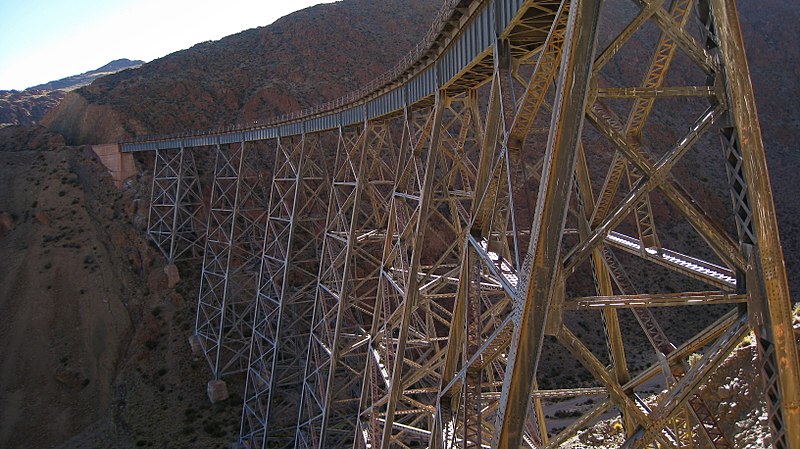
P>Ponte de aço. Fonte: Wikimedia Commons
Iron é a espinha dorsal do mundo que construímos à nossa volta e é o ingrediente básico do aço (ferro mais carbono). O ferro é um metal muito útil porque pode ser misturado com outros metais para fazer toda uma variedade de “ligas” que são ainda mais fortes e não enferrujam facilmente e podem ser moldadas em produtos desde carros a pinos, electrodomésticos a edifícios, pontes a caminhos-de-ferro, latas de comida a ferramentas. Em suma, dependemos do ferro (como aço) para fazer quase tudo o que precisamos para viver no século XXI. Hoje utilizamos vinte vezes mais ferro (sob a forma de aço) do que todos os outros metais juntos.
Iron (Fe) é um dos elementos formadores de rochas mais abundantes, constituindo cerca de 5% da crosta terrestre. É o quarto elemento mais abundante, depois do oxigénio, silício e alumínio e, depois do alumínio, o metal mais abundante e amplamente distribuído. O campo magnético da Terra deve-se ao ferro (e ao níquel) no seu núcleo, pelo que quando usamos uma bússola estamos a fazer uso do ferro que se encontra debaixo de nós. O ferro é um metal cinzento prateado que enferruja rapidamente quando exposto ao ar e à água. É responsável pela cor vermelha em muitas das nossas rochas e pelas areias vermelhas profundas dos desertos australianos. O ferro não é normalmente encontrado em forma pura dentro das rochas, mas sim combinado com oxigénio em minerais de minério como a hematite (da palavra grega que significa “pedra sanguínea”).
Propriedades
Na crosta terrestre o ferro é encontrado principalmente como minerais de óxido de ferro como a hematite, magnetite, goetite e limonite. Os minerais que são mais utilizados como minério para fazer ferro são a hematite (Fe2O3) e a magnetite (Fe3O4). O ferro é bastante macio e fácil de trabalhar, mas tem um ponto de fusão muito elevado de 1538°C. O ferro e algumas ligas de ferro são também magnéticos.
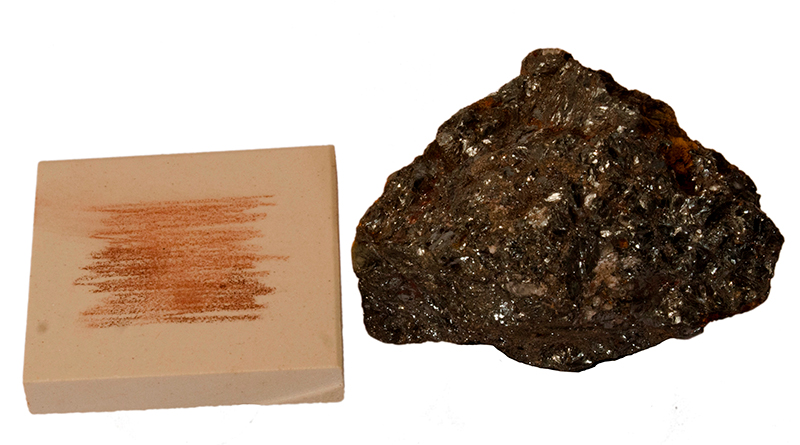
P>Pó de hematita e hematita em placa de listras. Fonte: Geoscience Australia
Iron é cerca de oito vezes mais pesado que a água (a sua densidade relativa é 7,87). Quando o ferro é exposto ao ar começa a transformar-se novamente em óxido de ferro e o pó vermelho que se forma na superfície do ferro é o que chamamos ferrugem. Pode ter-se visto ferrugem em carros velhos ou em barracões de ferro velhos. Para tornar o ferro mais forte e menos susceptível de enferrujar, pode ser combinado com carbono e outros elementos para fazer aço. O aço é um dos produtos mais reciclados do mundo, com cerca de 60% do aço disponível para reciclagem a voltar a fabricar aço novo.
>p>4 na escala de Mohs
>>p>2862°C
The Properties of Iron |
|
---|---|
>p>Símbolo químico>>p>p>Fe, vem da palavra latina para ferrum ferro | |
Ore |
p> Óxidos de ferro e.g. hematite e magnetite |
Densidade relativa |
p>7.87 g/cm3 |
Dureza |
|
p>Malleabilidade |
elevada |
p>Ductilidade>/td>>>p>elevada>/td> | |
p> Ponto de fusão |
1538°C |
Ponto de rebaixamento |
Usos
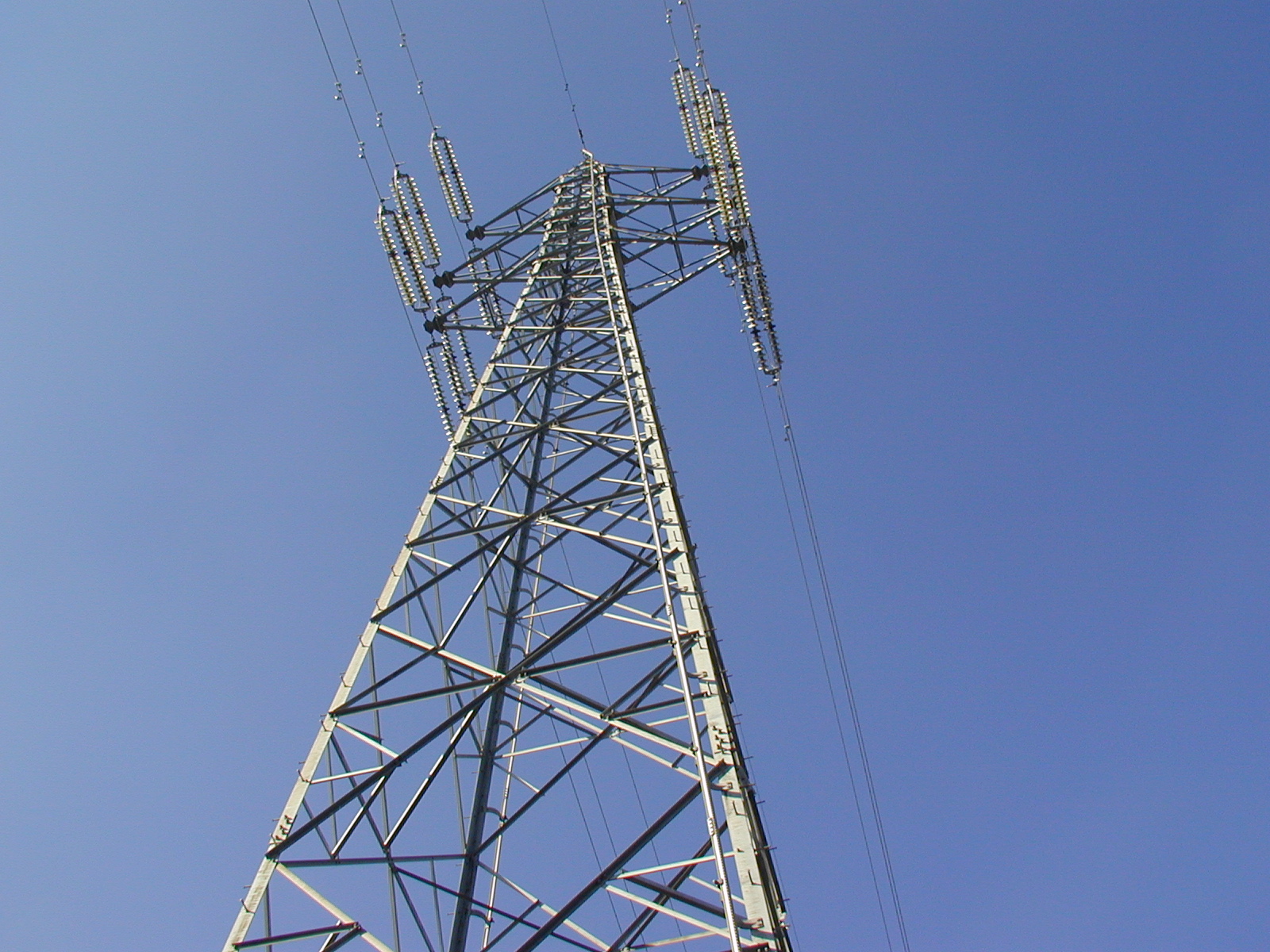
Pylon de aço suspendendo linhas eléctricas aéreas. Fonte: Wikimedia Commons
Sobre 98% da produção mundial de minério de ferro é utilizada para fazer ferro sob a forma de aço. O ferro em forma de fundição tem muitas utilizações específicas (por exemplo, tubos, acessórios, blocos de motor) mas o ferro puro é bastante macio. A adição de uma pequena quantidade de carbono (geralmente inferior a 1%) torna o ferro em aço, que é significativamente mais duro e extremamente versátil. Existem muitos tipos diferentes de aço feitos pela adição de carbono juntamente com outros elementos como o crómio, manganês, níquel, molibdénio para formar uma gama de ligas com propriedades diferentes (por exemplo, aço inoxidável). Ao alterar as proporções destes elementos adicionais, é possível fazer aços adequados para uma grande variedade de utilizações. A tabela abaixo mostra as propriedades e utilizações especiais de alguns compostos de ferro.
> nome do composto de ferro>p>ferro + até 5% carbono
Às vezes 1-3% silício
>>p>cutlery
hospital equipamento
peças de veículos motorizados>/td>
>>p>muito duro
muito quebradiço/td>>>p>ferramentas de corte de metal
bocados de perfuração/td>
principais componentes | properties | usos | |
---|---|---|---|
p>ferro fundido | p>rusts facilmente hard br>br>brittle>>>p>camp fornos blocos de cilindros de motor woks/td> |
||
ferro galvanizado |
ferro + revestimento de zinco |
resistente à ferrugem |
telhado |
Placa de estanho | ferro + revestimento de estanho | resistente à ferrugem | latas de conserva de alimentos |
p>Aço>/td>>>>p>ferro + menos de 1% carbono | >p>duro forte malleável>/td> maquinaria transporte cans &containers electrodomésticos/td> |
||
p>ferro + carbono níquel crómio>/td>>>p>doesn’t rust malleable |
|||
p>Aço para ferramentas>/td>>>p>ferro + carbono vanádio, crómio tungsténio e/ou molibdénio |
As propriedades desejáveis do aço e o seu custo relativamente baixo fazem dele o principal metal estrutural em projectos de engenharia e construção, representando cerca de 90% de todo o metal utilizado em cada ano. Cerca de 60% dos produtos de ferro e aço são utilizados no transporte e construção, 20% no fabrico de maquinaria, sendo o restante em latas e contentores (nas indústrias petrolífera e do gás) e em vários aparelhos e outros equipamentos, ver quadro abaixo para outras utilizações do ferro e do aço.
>p>Construção>/td>>>>p>P>Aço edifícios, pontes (como a ponte do porto de Sydney), reforços em edifícios de betão, coberturas, revestimentos, portas, vedações. >>>p>>p>Petróleo e gás>>>p>p> Varetas de perfuração de aço, invólucros, condutas. >p>Appliances and equipment>>p>>p>Frigoríficos de aço, máquinas de lavar roupa, máquinas de lavar louça, cutelaria, equipamento hospitalar./td>>>p>>p> O ferro puro é necessário para o crescimento adequado das plantas.
Animais necessitam de ferro para produzir energia e transportar sangue à volta do corpo (os alimentos ricos em ferro incluem carne vermelha e fígado, gemas de ovo e vegetais verdes de folhas). O ferro foi o primeiro elemento a ser reconhecido como essencial para as pessoas. Um médico em 1681 utilizou com sucesso o ferro para tratar pacientes que estavam pálidos, com falta de energia e que sofriam de anemia.
p>Cloreto de ferro é utilizado no tratamento e purificação da água.
>th> Utilização | Descrição |
---|---|
p>Transporte | p>Steel railway carriages/engines, navios, chassis de automóveis, cilindros de motores. |
p>Maquinaria>/td>>>>p> Motores de aço, bombas, gruas, equipamento de oficina (por exemplo ferramentas de corte, brocas de perfuração)./td> | |
p> Produtos de arame >/td>>>p>Vedações de arame de aço, cabos de navios, agrafos, telas de porta, porcas & parafusos. | |
p> Armazenamento>/td>>>p>p>containers de aço para alimentos, tanques de armazenamento.>/td> | |
p>Saúde | |
Fun >/td>> p> Os limalhas de ferro são utilizados em ‘sparklers’. |
|
p>Electrónica | >p> O cloreto de ferro é utilizado para gravar o cobre na fabricação de circuitos eléctricos impressos. |
p> Cozinhar >/td>>>p>p>Fornos e woks em ferro fundido para campismo.>/td> | |
p>Decoração>/td>>>p>Mobiliário de exterior em ferro forjado, gradeamentos de alpendre e outros artigos decorativos. |
História
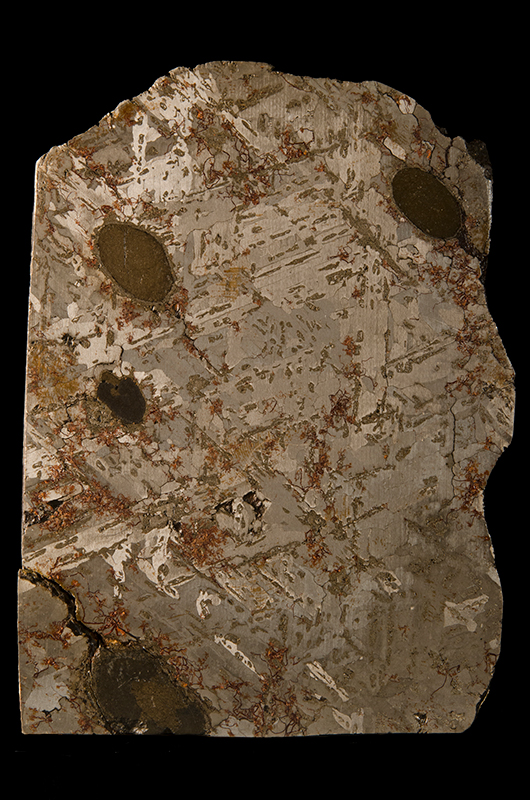
Meteoritooolac – meteorito de ferro. R21381. Fonte: Geoscience Australia
Iron está entre os metais mais antigos conhecidos pelos humanos. O Homem Paleolítico usou hematita finamente moída como tinta corporal. Por volta de 4000 AC, os egípcios e sumérios usaram pela primeira vez ferro de meteoritos para fazer contas, ornamentos, armas e ferramentas. A linha temporal da Idade do Ferro variou geograficamente; por exemplo, os Hittites forjaram ferro (aqueceram-no, depois martelaram-no, depois arrefeceram-no rapidamente para produzir ferro mais duro do que o bronze que as pessoas tinham usado antes) por volta do período de 1300 – 1100 a.C. e de forma semelhante, de acordo com Tewari (2003), as provas arqueológicas indicam que o trabalho com ferro na Índia ocorreu por volta de 1800 a 1000 a.C. Na época do Império Romano, o ferro estava a ser utilizado para camas, portões, carruagens, pregos, serras, machados, lanças, anzóis e ferramentas para afiar. Durante a Idade Média, com a introdução do canhão de ferro e da bola de canhão, o consumo de ferro aumentou para ultrapassar o cobre e o bronze como o metal mais amplamente utilizado. No final do século XIX começou a Idade do Aço, com navios de madeira a darem lugar ao aço, maquinaria a chegar às fábricas e a invenção da ferrovia. O ferro é indispensável à civilização moderna e as pessoas têm sido competentes na sua utilização há mais de 3.000 anos. Contudo, a sua utilização só se generalizou no século XIV, quando os fornos de fundição (o precursor dos altos-fornos) começaram a substituir as forjas.
Formação
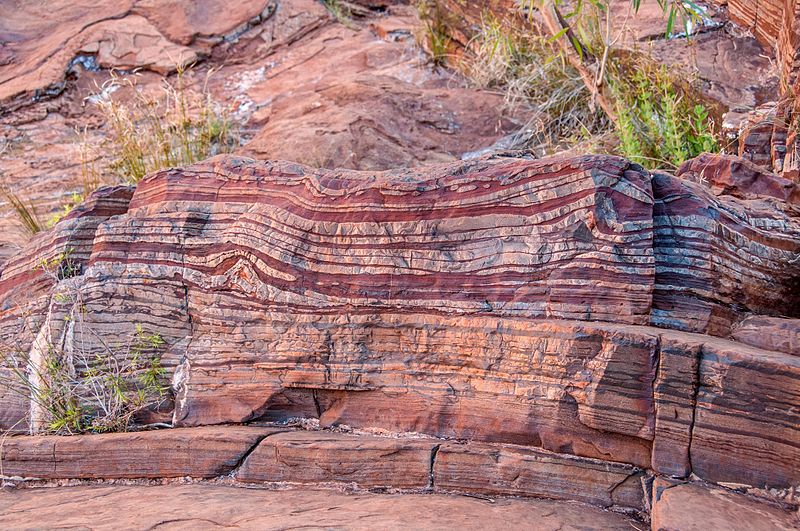
Formação de ferro cinzento em Fortescue Falls, Austrália Ocidental. Fonte: Wikimedia Commons
Os minérios de ferro são rochas das quais o ferro metálico pode ser extraído economicamente. A maioria dos depósitos de minério de ferro no mundo encontram-se em rochas conhecidas como formações de ferro em bandas (BIFs). Estas são rochas sedimentares que têm camadas alternadas de minerais ricos em ferro e uma rocha de sílica de grão fino chamada cerne.
Muitas das formações de ferro em bandas que estão a ser extraídas hoje em dia foram formadas há milhões de anos. Há cerca de 3000 milhões de anos atrás, não havia oxigénio ou havia muito pouco oxigénio dissolvido nos oceanos. No entanto, os oceanos continham muita sílica dissolvida, que provinha da intempérie das rochas. De vez em quando, esta sílica precipitava da água do mar como camadas de geleia de sílica, que lentamente se endurecia para se tornar a rocha a que chamamos cerne. O óxido de ferro solúvel foi também produzido a partir da desagregação das rochas e foi também lavado no mar pelos rios.
A cerca de 2500 milhões de anos atrás os oceanos eram habitados por bactérias que desenvolveram a capacidade de fotossintetizar e produzir oxigénio. Houve “florescimentos” sazonais que libertaram enormes quantidades de oxigénio para a água do mar que reagiram com o óxido de ferro solúvel para formar óxido de ferro insolúvel. Isto precipitou para fora da solução como os minerais magnetite e hematite formando camadas de ferro entre as outras camadas de sedimentos no fundo do mar.
Durante muitos milhões de anos estes processos de precipitação de sílica e óxido de ferro foram repetidos vezes sem conta resultando na deposição de camadas alternadas de inerte, hematite e magnetite. O nome formação de bandas de ferro provém da característica banda de cor destes enormes depósitos. O processo continuou durante quase mil milhões de anos e acabou por deixar acumular oxigénio na atmosfera.
Recursos
A maior parte dos importantes recursos mundiais de minério de ferro ocorre em formações de ferro em bandas, que são quase exclusivamente da idade pré-cambriana (ou seja, com mais de 541 milhões de anos). Os BIFs ocorrem em todos os continentes.
Iron foi o primeiro metal a ser descoberto na Austrália pelo explorador Edward John Eyre na cordilheira Middleback no Sul da Austrália. Embora os recursos de minério de ferro ocorram em todos os Estados e Territórios da Austrália, quase 90% dos recursos identificados ocorrem na Austrália Ocidental, incluindo quase 80% na província de Hamersley, uma das maiores regiões produtoras de minério de ferro do mundo. A Austrália é um dos maiores produtores de minério de ferro do mundo e o minério de ferro é a base de uma das principais indústrias de exportação da Austrália.

As principais jazidas e minas de ferro da Austrália (2016). Fonte: Geoscience Australia
Na cordilheira Hamersley, no distrito de Pilbara na Austrália Ocidental, existem três tipos principais de depósitos de ferro: enriquecimento de óxido de ferro dentro de BIFs, por exemplo Mt Tom Price; óxidos de ferro depositados ao longo de canais de rios antigos, principalmente da era terciária (paleocanais); e depósitos de óxido de ferro formados a partir da erosão de corpos de minério existentes (depósitos de minério de ferro detrital).
Os depósitos de enriquecimento BIF, incluindo hematite e hematite goetite são os mais importantes no que diz respeito a recursos e produção. O teor de ferro destes minérios varia muito e até recentemente a maioria dos depósitos necessitava de ter um grau médio de ferro superior a 60% para que a extracção fosse comercialmente viável. No entanto, alguns depósitos podem agora ter um teor de ferro entre 56%-59% de ferro e ser comercialmente viáveis. Os depósitos de enriquecimento BIF ocorrem na Austrália Ocidental no Pilbara (por exemplo Yarrie), e no Bloco Yilgarn (por exemplo Koolyanobbing) e no Sul da Austrália (por exemplo Iron Duke, Middleback Range). Os depósitos de paleocanais compostos de limonite pisolítica são os próximos em importância e são valorizados pelas suas baixas impurezas, tais como o fósforo. Não são tão ricos em ferro como os minérios de enriquecimento BIF. Os minerados contêm normalmente 57%-59% de ferro. Depósitos detríticos de minério de ferro são encontrados em declive dos depósitos de enriquecimento BIF a partir dos quais foram corroídos. São geralmente facilmente recuperados e têm uma qualidade entre 40%-55% de ferro.
Outras informações sobre recursos e produção.
Mineração
Formação de ferro em Fortescue Falls, Oeste da Austrália. Fonte: Wikimedia Commons
A maior parte dos minérios de ferro extraídos actualmente compreendem os minerais de óxido de ferro hematita, Fe2O3 (70% Fe); goetite, Fe2O3s H2O, (63% Fe); limonite, uma mistura de óxidos de ferro hidratados (até 60% Fe); e magnetite, Fe3O4 (72% Fe). Tal como a maioria das minas de minério de ferro em todo o mundo, todas as principais minas de minério de ferro australianas são cortadas a céu aberto. A rocha que suporta o minério de ferro é primeiro jateada e escavada a partir de minas a céu aberto. Os minérios das principais minas da região de Pilbara na Austrália Ocidental são transportados de faces de trabalho para fábricas de britagem e peneiramento, utilizando camiões que podem transportar mais de 300 toneladas. Existem três grandes produtores de minério de ferro de Pilbara: BHP Billiton Ltd (BHP), Rio Tinto Ltd (Rio) e Fortescue Metals Group Ltd (FMG).
Processamento
Processamento de minério de magnetita e hematita inclui trituração, peneiramento e moagem para produzir caroços de hematita e finos. O minério de magnetite é processado posteriormente através da separação magnética, um processo importante na produção de concentrado de ferro de magnetite.
Concentração inclui todos os processos que irão aumentar (melhorar) o teor de ferro de um minério através da remoção de impurezas. A beneficiação, um termo ligeiramente mais amplo, inclui estes processos, bem como aqueles que tornam um minério mais utilizável através da melhoria das suas propriedades físicas (por exemplo, peletização e sinterização). Muitas das minas de minério de ferro empregam alguma forma de beneficiação para melhorar a qualidade e as propriedades dos seus produtos. Em muitas minas em funcionamento, incluindo Mount Tom Price, Paraburdoo, Mount Whaleback e Christmas Creek, foram construídas instalações de beneficiamento de minério de ferro de baixa qualidade, incluindo minérios que foram contaminados com xisto, para serem extraídos e, após a sua modernização, vendidos como produtos de alta qualidade.
A peletização é um processo de tratamento utilizado para minérios muito finos ou em pó. Os pellets são uma alimentação ideal para alto-forno porque são duros e de tamanho e forma regulares. Na Austrália, os concentrados bombeados de Savage River são peletizados em Port Latta para serem expedidos para os mercados domésticos e ultramarinos e os minérios finos Middleback Range são peletizados antes da fundição no alto-forno Whyalla.
Sinterização é um processo utilizado para aglomerar finos de minério de ferro em preparação para a fundição de altos-fornos e é normalmente realizado em centros de produção de ferro e aço. Envolve a incorporação de calcário triturado, coque e outros aditivos disponíveis nas operações de produção de ferro e aço. Estes aditivos incluem resíduos extraídos de gases de escape do forno, escamas produzidas durante operações de laminagem e finos de coque produzidos durante a peneiração de coque.
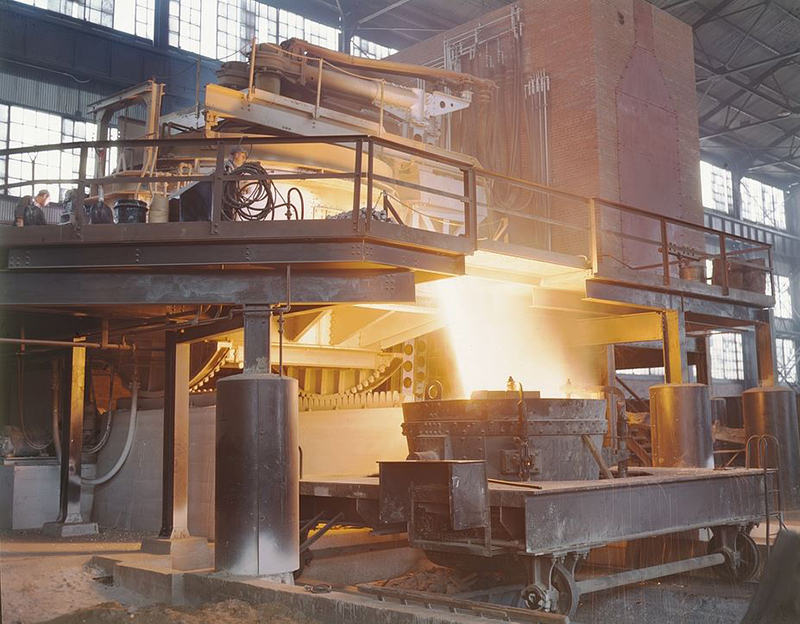
Aço branco-quente vertido de um forno de arco eléctrico. Fonte: Wikimedia Commons
Ferro-gusa é uma etapa intermédia na produção de aço e é produzido por fundição de minério de ferro (normalmente sob a forma de grumos, pellets ou sinterização) em altos-fornos. Os altos-fornos na Austrália estão localizados em Port Kembla e Whyalla. A remoção, por oxidação, de impurezas no ferro gusa, tais como silício, fósforo e enxofre e a redução do teor de carbono, resulta na produção de aço.
Adicionar metais como o níquel, crómio, manganês ou titânio dá ao aço propriedades especiais como resistência eléctrica e resistência ao desgaste, ferrugem, impacto, choque ou expansão quando aquecido.O aço arrefecido tem forma e pode ser revestido com estanho, zinco ou tinta para ajudar a protegê-lo da ferrugem, criando produtos como o Zincalume e o Colorbond.